The technologies biopharmaceutical manufacturing needs to deliver new product types
Billy Sisk, Life Sciences Industry Leader EMEA at Rockwell Automation discusses the increasing adoption of disruptive technology in the manufacturing process
Add bookmark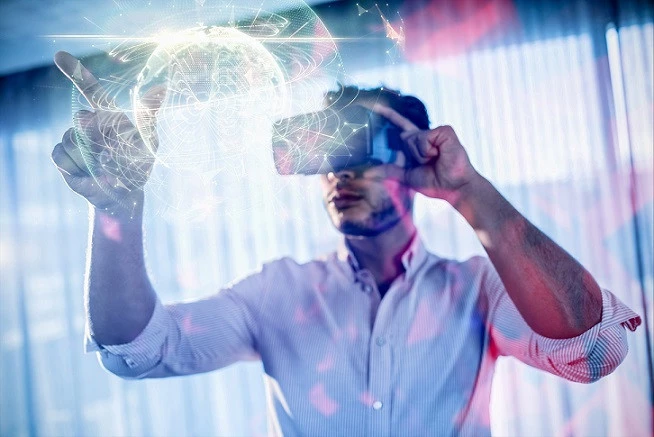
In recent years, there has been a paradigm shift in the biopharmaceutical manufacturing space away from blockbuster treatments toward personalized therapies for smaller patient groups.
These complex, highly targeted treatments, such as biologics and cell and gene therapy, can be lucrative but present a number of challenges in the manufacturing process.
The manufacturing of these products is far more complicated than traditional treatments and can operate on tightly controlled timeframes. We have recently been hearing increasing discussion of therapeutics requiring the process of production to infusion to take place in a matter of hours. To deliver this speed of treatment, far more small-scale, regional manufacturing hubs will be necessary.
To meet changing market demands, manufacturers are realizing that technology will be a critical component of the process.
What are some of the early applications of artificial intelligence?
When you look at the typical manufacturing environment, the average age of industrial equipment is over 20 years old. This legacy technology does not often lend itself well to the demands of next-generation biologics. If companies want to be able to bring these new medicines to market in a cost-effective way, innovative technology will need to be adopted.
Hype has been growing in the industry around the topic of artificial intelligence (AI), with 55 of the top 60 pharmaceutical manufacturers now officially partnered with AI companies. A key area of interest for AI in the manufacturing process is the ability of predictive maintenance algorithms to spot and resolve equipment issues early on to avoid costly shutdowns. With a skills gap on the horizon, the process of democratizing maintenance knowledge to staff with lower levels of experience is highly appealing to manufacturers looking to improve the efficiency of their operations.
Is there growing interest in augmented reality technology?
There has also been an explosion of interest in augmented reality (AR). Equally driven by concerns around the high number of skilled staff set to exit the labor force in the coming years, AR can transform staff knowledge into digestible training formats, such as the recording of routine tasks via smart glasses to then be readily available as training materials.
This process can also reveal areas of inefficiency in current manufacturing operations. A top five global pharmaceutical manufacturer shared a recent example of a project undertaken to video record 500 staff members completing the same task. They discovered that all 500 members of staff were performing the task in a different way. When a relatively simple task is performed differently, this can lead to losses in productivity and can raise concerns from auditors, opening manufacturers to increased regulatory and quality risk. Through the use of AR, this manufacturer has been able to distill the task into a clear standard operating procedure for all workers to follow, eliminating the risk.
With manufacturing operations also becoming more flexible and increasing the adoption of single-use equipment, the process of connecting facility equipment is far more difficult for operators. AR can help to improve digital assembly and ensure the correct set-up is being followed by providing a clear, equipment specific guide and logging the process in real time. When digital instructions are given, workers are able to build and administer the production process in a faster and more consistent manner.
Greater adoption of disruptive technology in manufacturing
If you consider the cost involved from a plant shutdown or a system failure from a faulty connection or poor set-up, it can easily run into the tens of millions of dollars. In the context of these costs from error, the technology to address this problem can more easily prove return on investment.
While AI may require specific effort and skillsets to organize, clean and utilize the right data, AR can offer a quick implementation process from use case to scale-up. As it does not require a plant interruption, there is also no negative impact on production, scheduling or the efficiency of the facility.
With change clearly on the horizon for the manufacturing process and technology starting to prove its effectiveness, the industry must be ready to adopt and implement the tools needed to make them an effective market player.
Find out more about Rockwell Automation here.